CNC Milling Services
Get quality custom parts for prototyping and production, fast and cost-effective.
Materials
Aluminum | Stainless Steel | Steel | Other Metals | Plastics |
2024 | 303 | 1018 | Copper 101 | ABS |
5052 | 304/304L | 1215 | Copper 260 | Acetal (Delrin) |
6061 | 316/316L | 4130 | Copper 360 | Polycarbonate |
6063 | 410 | 4140 | Copper C110 | PET |
7050 | 416 | 4140PH | Copper C932 | PA66 (Nylon) |
7075 | 420 | 4340 | Inconel 718 | PEEK |
440C | A36 | Titanium (Grade 2) | PTFE (Teflon) | |
15-5 | Titanium (Grade 5) | Polypropylene | ||
17-4 | Zinc Alloy | POM | ||
18-8 | PTFE | |||
Nitronic 60 (218 SS) | PMMA |
* We can source any other materials on request.
CNC Milling Finishes
Standard. With no secondary processing.
Anodizing is an electrochemical process that converts the metal surface into a decorative, durable, corrosion-resistant, anodic oxide finish.
Aluminum is ideally suited to anodizing, although other nonferrous metals, such as magnesium and titanium, also can be anodized.
The bead blasting process shoots a blasting media – beads – under high pressure at a part to clean, polish, or roughen it to the desired finish.
A bead blast finish can clean a part’s surface, remove cosmetic defects, create a uniform surface with a dull, satin, or rough texture, and even harden a part’s surface and enhance its durability. It also prepares a part for paint and other coatings.
Bead media includes steel, glass, quartz sand, garnet, etc.
Manufacturers apply bead blasting for materials like metals, plastics, rubber, and glass.
Electrophoresis is the process of applying paint to parts by passing an electric current through the paint solution and parts immersed in it.
In many ways, this process is similar to electroplating. It is also called electrocoating, e-coating, electrophoretic coating, and electrophoretic painting.
Electrophoresis is suitable for aluminum alloy, zinc alloy, and stainless steel. It makes the parts present various colors and keep the metallic luster, and enhances the surface performance with high corrosion resistance.
Electroplating is the process of applying a thin layer of one metal to a part by passing a positively charged electrical current through a solution containing dissolved metal ions (anode) and a negatively charged electrical current through the part to be plated (cathode).
The aim is to improve the overall quality of the part. Some benefits include improving corrosion resistance, wear resistance, appearance, lubricity, and solderability.
Steels, nickel, copper-based alloys, and other metals are readily electroplated.
Polishing is the process of creating a shiny and smooth surface, either through physical rubbing of the part or by chemical interference.
The process enhances the aesthetic appeal, prevents corrosion, improves cleanability, and reduces adhesion of the parts.
It produces a surface with significant specular reflection but can reduce diffuse reflection in some materials.
Polishing works excellent with many metals, including aluminum, brass, stainless steel, and steel.
Powder coating is a process of applying a free-flowing, dry, thermoset, or thermoplastic powder to the surface of a part which is then cured under heat or with ultraviolet light.
The process creates a strong, wear- and corrosion-resistant layer that is more durable than standard painting methods.
It works perfectly on metals, plastics, and other materials.
Don’t see the finish you need? Please submit a RFQ, and we will look into a finishing process for you.
CNC Milling Capabilities
Metric | Imperial | |
Max. Part Size | Ø1000 x 1500 mm | Ø393.70 x 590.55 in |
Tolerance | ±0.025 mm | ±0.001 in |
Tolerances: ISO 2768 unless otherwise specified.
What is CNC Milling?
CNC milling is a manufacturing process in which computer-controlled cutting tools mounted on a rotating spindle remove material from a workpiece. The workpiece is mounted to a table that moves or rotates on different planes so the tool can work on it at many angles.
Advantages of CNC Milling
Capable of creating a range of different shapes
High precision
Very fast
High efficiency
Wide range of material options
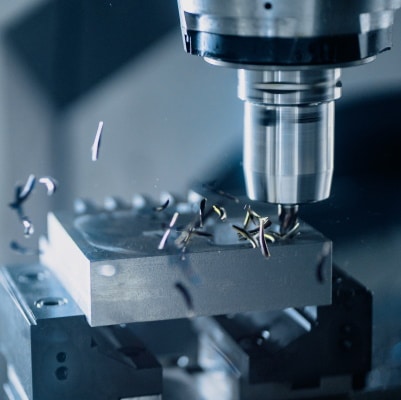
CNC Milling FAQs
CNC machines must be programmed to allow offsets for the diameter and length of the tool to cut the part. By knowing the exact tool offsets a machinist can find the precise machining starting point.
A CNC router moves the spindle around a stationary table and is primarily designed to operate at high speeds.
A CNC mill typically moves the workpiece along a linear axis, making cuts through the driving force of rotational speed.
The most commonly used materials in CNC milling are metals, such as aluminum, brass or steel and plastics such as ABS, acrylic, polycarbonate, and polypropylene.