Metal Injection Molding Services
Get quality custom parts for prototyping and production, fast and cost-effective.
Metal Injection Molding Materials
Stainless Steel | Tool Steel | Low Alloy Steel | Soft Magnetic Steel | Tungsten Heavy Alloy | Low Expansion Alloy | WC-Co Cemented Carbide |
303 | M2 | Fe-2Ni | Fe-Ni50 | Fe-Ni90 | Kovar | WC-Co (6%) |
304 | 42CrMo4 | Fe-2Ni-0.5C | Fe3Si | W-Fe-Ni92 | Invar | WC-Co (Tungsten carbide-cobalt) |
316/316L | Fe-2Ni-0.5C-HT | FeCo50 | 5W-Fe-Ni9 | |||
420P | Fe-8Ni | FeCoV | W-Ni-Fe (Tungsten Nickel Iron) | |||
430L | SAE 4650 | W-Ni-Cu (Tungsten Nickel Copper) | ||||
440C | Fe-Ni | |||||
440C-HT | FN02 | |||||
17-4PH | FN08 | |||||
17-4PH -HT | 4140 | |||||
8620 | ||||||
100Cr6 |
* We can source any other material on requests.
Metal Injection Molding Finishes
Standard. With no secondary processing.
The bead blasting process shoots a blasting media – beads – under high pressure at a part to clean, polish, or roughen it to the desired finish.
A bead blast finish can clean a part’s surface, remove cosmetic defects, create a uniform surface with a dull, satin, or rough texture, and even harden a part’s surface and enhance its durability. It also prepares a part for paint and other coatings.
Bead media includes steel, glass, quartz sand, garnet, etc.
Manufacturers apply bead blasting for materials like metals, plastics, rubber, and glass.
Electrophoresis is the process of applying paint to parts by passing an electric current through the paint solution and parts immersed in it.
In many ways, this process is similar to electroplating. It is also called electrocoating, e-coating, electrophoretic coating, and electrophoretic painting.
Electrophoresis is suitable for aluminum alloy, zinc alloy, and stainless steel. It makes the parts present various colors and keep the metallic luster, and enhances the surface performance with high corrosion resistance.
Electroplating is the process of applying a thin layer of one metal to a part by passing a positively charged electrical current through a solution containing dissolved metal ions (anode) and a negatively charged electrical current through the part to be plated (cathode).
The aim is to improve the overall quality of the part. Some benefits include improving corrosion resistance, wear resistance, appearance, lubricity, and solderability.
Steels, nickel, copper-based alloys, and other metals are readily electroplated.
Polishing is the process of creating a shiny and smooth surface, either through physical rubbing of the part or by chemical interference.
The process enhances the aesthetic appeal, prevents corrosion, improves cleanability, and reduces adhesion of the parts.
It produces a surface with significant specular reflection but can reduce diffuse reflection in some materials.
Polishing works excellent with many metals, including aluminum, brass, stainless steel, and steel.
Powder coating is a process of applying a free-flowing, dry, thermoset, or thermoplastic powder to the surface of a part which is then cured under heat or with ultraviolet light.
The process creates a strong, wear- and corrosion-resistant layer that is more durable than standard painting methods.
It works perfectly on metals, plastics, and other materials.
Metal Injection Molding Capabilities
Metric | Imperial | |
Max. Part Size | ≦ 4000 mm | ≦ 157.48 in |
Min. Wall Thickness | 0.7 mm | 0.03 in |
Max. Part Weight | 1500 g | 3.31 lb |
Min. Part Weight | 5 g | 0.18 oz |
Tolerances: ISO2768
What is Metal Injection Molding?
Metal injection molding (MIM) is a manufacturing process in which polymerized metal powders are injected into molds, de-binded, and sintered, to produce smaller, complex metal parts in high volume.
Advantages of Metal Injection Molding
Cost-effective manufacture of high-volume complex parts
Excellent mechanical properties reflecting fine particle size and high sintered density
Wide range of pre-alloys and master alloys available
Minimum of finishing operations
Net-shape manufacture with minimal material waste (runners, sprues recyclable in-house)
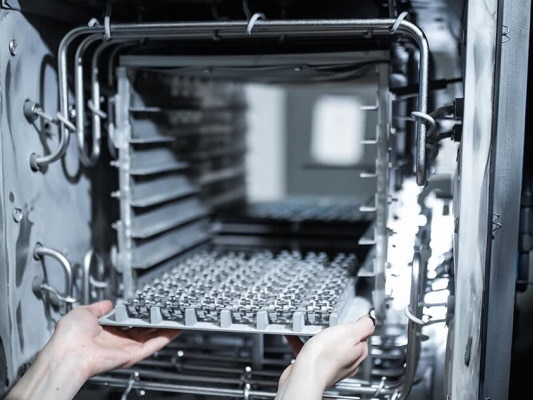
Metal Injection Molding FAQs
As-sintered tolerances typically range from ±0.3%-0.5% of the dimension. The tolerance capability is mainly dependent on multiple variables, including part geometry, material, mold construction, etc.
Our partners can incorporate secondary machining operations after sintering to achieve tolerances tighter than the typical tolerances the process can produce. Parts designed specifically for the MIM process are ideal for cost and time savings, as secondary operations can significantly affect these factors.
The most common limiting factor with MIM is part size. Due to mold limitations and economics, MIM is typically best suited for parts that weigh less than 100 grams and can fit in the palm of your hand.
Part quantity can also be a limitation. To take advantage of the potential cost savings compared to other processes, you will generally need to order a high quantity of parts to offset upfront tooling costs with MIM.
MIM is optimal for high-volume production and not suitable for prototyping. However, Xometry offers many other processes, such as direct metal laser sintering (DMLS) or metal binder jetting, which are excellent options for prototyping metal parts!
Final parts typically fall in a density range of 96%-99% and will be water-tight.
Parts will shrink roughly 20% from the molded state to the post-sintered state. The shrink factor is usually accounted for during mold creation by the manufacturer, so your designed dimensions should reflect your final part requirements.
Generally speaking, parts with higher complexity, lots of dimensions, small in size (~100g or less), and quantities that would be cost-prohibitive to produce in other manufacturing processes are good criteria for MIM consideration. MIM is also excellent for consolidating designs that usually require assembly and instead be made as one component. Our industry experts will be happy to work with you to help you determine if MIM is right for you!