Sand Casting Services
Get quality custom parts for prototyping and production, fast and cost-effective.
Parts Proudly Manufactured Through Us
Sand Casting Materials
Aluminum | Ductile Iron | Grey Iron | High SiMo-Ductile Iron |
A356 | EN-GJS-350-22/LT | EN-GJL-150 | EN-GJS-SiMO40-6 |
360 | EN-GJS-400-18/LT | EN-GJL-200 | EN-GJS-XSiMo5.10 |
A360 | EN-GJS-400-15 | EN-GJL-250 | |
380 | EN-GJS-450-10EN-GJS-500-7 | EN-GJL-300 | |
A380 | EN-GJS-550-5 | EN-GJL-350 | |
383 | EN-GJS-600-3 | ||
A383 | EN-GJS-700-2 | ||
384 | EN-GJS-800-2 | ||
384 | EN-GJS-500-10 | ||
413 | |||
A413 | |||
B390 |
* We can source any other materials.
Sand Casting Finishes
Standard. With no secondary processing.
Anodizing is an electrochemical process that converts the metal surface into a decorative, durable, corrosion-resistant, anodic oxide finish.
Aluminum is ideally suited to anodizing, although other nonferrous metals, such as magnesium and titanium, also can be anodized.
The bead blasting process shoots a blasting media – beads – under high pressure at a part to clean, polish, or roughen it to the desired finish.
A bead blast finish can clean a part’s surface, remove cosmetic defects, create a uniform surface with a dull, satin, or rough texture, and even harden a part’s surface and enhance its durability. It also prepares a part for paint and other coatings.
Bead media includes steel, glass, quartz sand, garnet, etc.
Manufacturers apply bead blasting for materials like metals, plastics, rubber, and glass.
Polishing is the process of creating a shiny and smooth surface, either through physical rubbing of the part or by chemical interference.
The process enhances the aesthetic appeal, prevents corrosion, improves cleanability, and reduces adhesion of the parts.
It produces a surface with significant specular reflection but can reduce diffuse reflection in some materials.
Polishing works excellent with many metals, including aluminum, brass, stainless steel, and steel.
Powder coating is a process of applying a free-flowing, dry, thermoset, or thermoplastic powder to the surface of a part which is then cured under heat or with ultraviolet light.
The process creates a strong, wear- and corrosion-resistant layer that is more durable than standard painting methods.
It works perfectly on metals, plastics, and other materials.
Sand Casting Capabilities
Metric | Imperial | |
Max. Part Size | ø 3000 mm | ø 118.11 in |
Min. Wall Thickness | 3.5 mm | 0.14 in |
Max. Part Weight | 5000 kg | 11023 lb |
Tolerances: NADCA Product Specification Standards
What is Sand Casting?
Sand casting is a process of making highly detailed and complex parts by pouring molten metal into sand-based molds. Certain sand casting parts require a secondary machining process.
Advantages of Sand Casting
Cost-effective manufacture of high-volume complex parts
Excellent mechanical properties reflecting fine particle size and high sintered density
Wide range of pre-alloys and master alloys available
Minimum of finishing operations
Net-shape manufacture with minimal material waste (runners, sprues recyclable in-house)
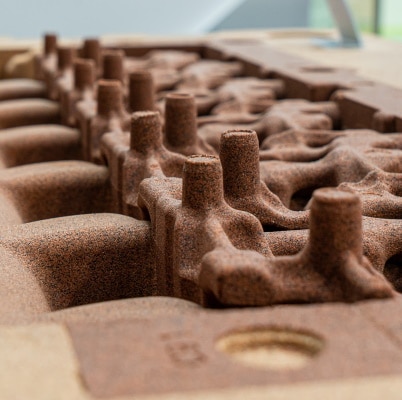
Sand Casting FAQs
Due to its exceptional versatility, sand casting is one of the most widely used manufacturing processes for a variety of applications, including:
- Construction equipment (housings, combustors, manifolds, gearboxes, transmission impellers)
- Engine components (housings, brackets, frames, pistons, cylinders, manifolds)
- Wind energy components (torque arms, rotor hubs, blades, axle pins)
- Agricultural applications (axles, gears, gearboxes, brake drums, pulleys)
Sand casting uses the following types of sand to produce molds:
- Green sand. Also known as clay, green sand molds are created using wet sand. The process is quick and efficient, and the sand can be reused.
- Resin sand. Resin sand is shaped using heat and exhibits a smooth surface when formed, so less finishing work is required.
Investment casting is similar to sand casting in that both methods use prefabricated breakable molds for casting finished parts from metal alloys.
While sand casting uses sand-based molds, investment casting uses melted heat-resistant material, often ceramic, coated around a wax pattern to create the mold.
While sand casting leaves a rough surface that requires more finishing, investment casting results in a smooth finish with minimal little machining necessary to produce a finished product. However, investment casting tends to come at a higher cost, as the mold material is more expensive and cannot be reused.
Die casting is the ideal choice for any complex project requiring high accuracy and a low margin of error. On the other hand, sand casting provides far more flexibility with size and is the perfect choice for large parts. The biggest advantage, however, is not its flexibility and low cost but rather sand casting is alloy friendly and can be used with any type, mostly without complications.