Metal Stamping Services
Get quality custom parts for prototyping and production, fast and cost-effective.
Parts Proudly Manufactured Through Us
Metal Stamping Finishes
Standard. With no secondary processing.
Anodizing is an electrochemical process that converts the metal surface into a decorative, durable, corrosion-resistant, anodic oxide finish.
Aluminum is ideally suited to anodizing, although other nonferrous metals, such as magnesium and titanium, also can be anodized.
The bead blasting process shoots a blasting media – beads – under high pressure at a part to clean, polish, or roughen it to the desired finish.
A bead blast finish can clean a part’s surface, remove cosmetic defects, create a uniform surface with a dull, satin, or rough texture, and even harden a part’s surface and enhance its durability. It also prepares a part for paint and other coatings.
Bead media includes steel, glass, quartz sand, garnet, etc.
Manufacturers apply bead blasting for materials like metals, plastics, rubber, and glass.
Electrophoresis is the process of applying paint to parts by passing an electric current through the paint solution and parts immersed in it.
In many ways, this process is similar to electroplating. It is also called electrocoating, e-coating, electrophoretic coating, and electrophoretic painting.
Electrophoresis is suitable for aluminum alloy, zinc alloy, and stainless steel. It makes the parts present various colors and keep the metallic luster, and enhances the surface performance with high corrosion resistance.
Electroplating is the process of applying a thin layer of one metal to a part by passing a positively charged electrical current through a solution containing dissolved metal ions (anode) and a negatively charged electrical current through the part to be plated (cathode).
The aim is to improve the overall quality of the part. Some benefits include improving corrosion resistance, wear resistance, appearance, lubricity, and solderability.
Steels, nickel, copper-based alloys, and other metals are readily electroplated.
Polishing is the process of creating a shiny and smooth surface, either through physical rubbing of the part or by chemical interference.
The process enhances the aesthetic appeal, prevents corrosion, improves cleanability, and reduces adhesion of the parts.
It produces a surface with significant specular reflection but can reduce diffuse reflection in some materials.
Polishing works excellent with many metals, including aluminum, brass, stainless steel, and steel.
Powder coating is a process of applying a free-flowing, dry, thermoset, or thermoplastic powder to the surface of a part which is then cured under heat or with ultraviolet light.
The process creates a strong, wear- and corrosion-resistant layer that is more durable than standard painting methods.
It works perfectly on metals, plastics, and other materials.
Metal Stamping Capabilities
Stamping part tolerance range: up to ± 0.01 mm
Tolerances: GB/T15055-2021
What is Metal Stamping?
Precision metal stamping is a manufacturing process that uses a stamping press fitted with a custom die to turn sheet metal into the desired precise parts at tight tolerances.
Advantages of Metal Stamping
Automated processes
Suited to produce high-volume complex parts
Consistent quality and high precision
Lower production costs
Less scrap material
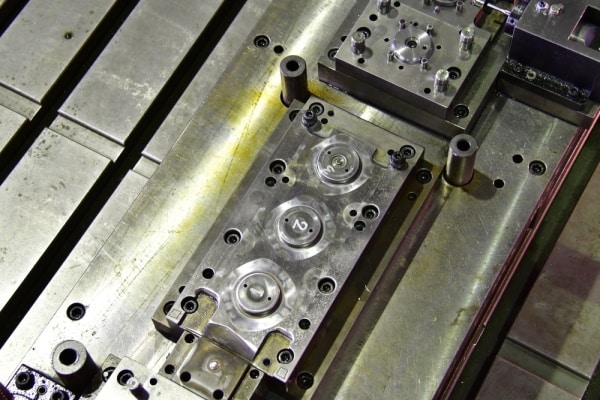
Metal Stamping FAQs
A “progressive die” is a series of punch press tools designed to perform all the punching, cutting, coining, and bending required to produce a metal part through a multi-step process. With a progressive die, metal blanks are fed through all stations of the progressive stamping die; each station performs one or more operations until the part is completed.
The two most significant factors that affect the price of stamped metal parts are material selection and tolerance complexity.
Specialty materials and alloys often greatly increase the stamped part costs. However, alternate materials can provide specified performance and significant savings.
Specifying a custom thicknesses material can also add to the cost. On the other hand, a “standard thickness” option will save money if it works to meet all tolerances and specifications.
Tolerance complexity can also affect the cost. Tight tolerances (with a variation of ± 0.005” or less) require more complex operations, including increased tooling maintenance. Often, complex tolerance designs also require secondary operations, further adding to the end-part cost.
Metal stamping encompasses a wide range of metal forming operations like bending, pressing, folding, and stretching, in addition to stamping. All metal stamping processes use punch presses with custom-made tooling and dies to produce a part’s desired shape, pattern, or other characteristics. Metal stamping can provide tighter tolerances than fabrication. It is a fast and cost-effective way to produce metal parts in large quantities.
Metal fabrication entails manufacturing three-dimensional metal parts via cutting, bending, and other assembly processes. Fabrication is usually performed on CNC laser cutters, press brakes, turret presses, and welding. Metal fabrication is often a more economical way to produce parts in lower quantities. Fabrication also provides greater design flexibility than stamping, as there is no tooling to change should your part design require alteration.